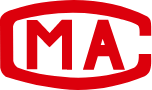



润滑剂分析相关标准参考信息
GB/T 23718.4-2015 机器状态监测与诊断 人员资格与人员评估的要求 第4部分:现场润滑剂分析
简介:
信息:ICS: CCS: 发布: 实施:2016-07-01
ASTM D7844-18 使用傅里叶变换红外(FT-IR)光谱法通过趋势分析对在线润滑剂中的烟灰进行状态监测的标准测试方法
简介:
信息:ICS:75.160.20 CCS: 发布:2018-01-01 实施:
ASTM D7844-12 使用傅里叶变换红外(FT-IR)光谱法通过趋势分析对在线润滑剂中的烟灰进行状态监测的标准测试方法
简介:
信息:ICS:75.160.20 CCS: 发布:2012-12-01 实施:
ASTM D7874-13(2022) 在用润滑剂试验中应用失效模式和影响分析(FMEA)的标准指南
简介:
信息:ICS:75.100 CCS: 发布:2022-10-01 实施:
ASTM D7414-18 通过趋势分析使用傅立叶变换红外(FT-IR)光谱测定法对在役石油和烃基润滑剂中氧化的状态监测的标准测试方法
简介:
信息:ICS:75.100 CCS: 发布:2018-01-01 实施:
ASTM D7343-12 用于石油产品和润滑剂元素分析的X射线荧光光谱法优化 样品处理 校准和验证的标准操作规程
简介:
信息:ICS:71.040.50 CCS: 发布:2012-12-01 实施:
ASTM D7844-22 使用傅立叶变换红外光谱法进行趋势分析的在用润滑剂中烟尘状态监测的标准试验方法
简介:
信息:ICS:75.160.20 CCS: 发布:2022-07-01 实施:
ASTM D7412-18 使用傅立叶变换红外(FT-IR)光谱法通过趋势分析对在役石油和烃基润滑剂中的磷酸盐抗磨添加剂进行状态监测的标准测试方法
简介:
信息:ICS:75.100 CCS: 发布:2018-01-01 实施:
ASTM D7260-12 用于石油产品和润滑剂元素分析的电感耦合等离子体原子发射光谱法(ICP-AES)的优化 校准和验证的标准实践
简介:
信息:ICS:75.080 CCS: 发布:2012-06-01 实施:
ASTM D8321-22 基于光谱测量预测石油产品、液体燃料和润滑剂性能用多元分析的开发和验证的标准实施规程
简介:
信息:ICS:75.080 CCS: 发布:2022-04-01 实施:
ASTM D8127-17e1 使用用于在线润滑剂的X射线荧光(XRF)的耦合颗粒和元素分析的标准测试方法
简介:
信息:ICS:75.100 CCS: 发布:2017-07-01 实施:
ASTM D7260-2012 石油产品和润滑剂的元素分析的感应耦合等离子体-原子发散光谱法 (ICP-AES) 的识别, 校正和最优化的标准实施规程
简介:Accurate elemental analysis of petroleum products and lubricants is necessary for the determination of chemical properties, which are used to establish compliance with commercial and regulatory specifications. Inductively Coupled Plasma-Atomic Emission Spectrometry is one of the more widely used analytical techniques in the oil industry for multi-element analysis as evident from at least twelve standard test methods (for example, Test Methods C1111, D1976, D4951, D5184, D5185, D5600, D5708, D6130, D6349, , D7040, D7111, D7303, and D7691) published for the analysis of fossil fuels and related materials. These have been briefly summarized by Nadkarni. The advantages of using an ICP-AES analysis include high sensitivity for many elements of interest in the oil industry, relative freedom from interferences, linear calibration over a wide dynamic concentration range, single or multi-element capability, and ability to calibrate the instrument based on elemental standards irrespective of their elemental chemical forms, within limits described below such as solubility and volatility assuming direct liquid aspiration. Thus, the technique has become a method of choice in most of the oil industry laboratories for metal analyses of petroleum products and lubricants.1.1 This practice covers information on the calibration and operational guidance for the multi-element measurements using inductively coupled plasma-atomic emission spectrometry (ICP-AES). 1.2 This standard does not purport to address all of the safety concerns, if any, associated with its use. It is the responsibility of the user of this standard to establish appropriate safety and health practices and determine the applicability of regulatory limitations prior to use.
信息:ICS:75.080 (Petroleum products in general); 75.100 (Lu CCS:E34 发布:2012 实施:
ASTM D8321-21 基于光谱测量预测石油产品、液体燃料和润滑剂特性用多元分析的开发和验证的标准实施规程
简介:
信息:ICS:75.080 CCS: 发布:2021-05-01 实施:
ASTM D8127-17 使用用于在线润滑剂的X射线荧光(XRF)的耦合颗粒和元素分析的标准测试方法
简介:
信息:ICS:75.100 CCS: 发布:2017-07-01 实施:
ASTM D7343-2012 石油产品和润滑剂元素分析用X射线荧光光谱法的优化, 制样, 校正和鉴定的标准实施规程
简介:3. Significance and UseTop Bottom 3.1 Accurate elemental analyses of samples of petroleum and petroleum products are required for the determination of chemical properties, which are in turn used to establish compliance with commercial and regulatory specifications. 1.1 This practice covers information relating to sampling, calibration and validation of X-ray fluorescence instruments for elemental analysis, including all kinds of wavelength dispersive (WDXRF) and energy dispersive (EDXRF) techniques. This practice includes sampling issues such as the selection of storage vessels, transportation, and sub-sampling. Treatment, assembly, and handling of technique-specific sample holders and cups are also included. Technique-specific requirements during analytical measurement and validation of measurement for the determination of trace elements in samples of petroleum and petroleum products are described. For sample mixing, refer to Practice D5854. Petroleum products covered in this practice are considered to be a single phase and exhibit Newtonian characteristics at the point of sampling. 1.2 Applicable Test Methods???This practice is applicable to the XRF methods under the jurisdiction of ASTM Subcommittee D02.03 on Elemental Analysis, and those under the jurisdiction of the Energy Institute???s Test Method Standardization Committee (Table 1). Some of these methods are technically equivalent though they may differ in details (Table 2).TABLE 1 XRF Standard Test Methods for Analysis of Petroleum Products and Lubricants Technique Analysis ASTM EI
信息:ICS:71.040.50 (Physicochemical methods of analysis) CCS:E34 发布:2012 实施:
ASTM D4927-20 用波长色散X射线荧光光谱法对润滑剂和添加剂成分进行元素分析的标准试验方法钡钙磷硫锌
简介:
信息:ICS:75.100 CCS: 发布:2020-12-01 实施:
ASTM D7260-17 用于石油产品和润滑剂元素分析的电感耦合等离子体原子发射光谱法(ICP-AES)的优化 校准和验证的标准实践
简介:
信息:ICS:75.080 CCS: 发布:2017-06-01 实施:
ASTM D7740-11 石油产品和润滑剂金属分析的原子吸收光谱法优化 校准和验证标准实践
简介:
信息:ICS:71.040.50 CCS: 发布:2011-07-01 实施:
ASTM D7844-20 使用傅里叶变换红外(FT-IR)光谱法通过趋势分析对在线润滑剂中的烟灰进行状态监测的标准测试方法
简介:
信息:ICS:75.160.20 CCS: 发布:2020-09-01 实施:
ASTM D7343-12(2017) 用于石油产品和润滑剂元素分析的X射线荧光光谱法优化 样品处理 校准和验证的标准操作规程
简介:
信息:ICS:71.040.50 CCS: 发布:2017-06-01 实施:
ASTM D7690-11 通过分析铁路从在役润滑剂的微粒表征的标准实践
简介:
信息:ICS:75.100 CCS: 发布:2011-01-01 实施:
ASTM D7343-20 用于石油产品和润滑剂元素分析的X射线荧光光谱法优化 样品处理 校准和验证的标准操作规程
简介:
信息:ICS:71.040.50 CCS: 发布:2020-07-01 实施:
ASTM D7690-11(2017) 通过分析铁路从在役润滑剂的微粒表征的标准实践
简介:
信息:ICS:75.100 CCS: 发布:2017-05-01 实施:
ASTM D7740-2011 金属分析石油产品和润滑剂的最优化,校准和原子吸收光谱法有效性的标准操作规程
简介:Accurate elemental analysis of petroleum products and lubricants is necessary for the determination of chemical properties, which are used to establish compliance with commercial and regulatory specifications. Atomic Absorption Spectrometry (AAS) is one of the most widely used analytical techniques in the oil industry for elemental analysis. There are at least twelve Standard Test Methods published by ASTM D02 Committee on Petroleum Products and Lubricants for such analysis. See Table 1.1.1 This practice covers information on the calibration and operational guidance for elemental measurements using atomic absorption spectrometry (AAS). 1.1.1 AAS Related Standards8212;Test Methods D1318, D3237, D3340, D3605, D3831, D4628, D5056, D5184, D5863, D6732; Practices D7260 and D7455; and Test Methods D7622 and D7623. 1.2 The values stated in SI units are to be regarded as standard. No other units of measurement are included in this standard. 1.3 This standard does not purport to address all of the safety concerns, if any, associated with its use. It is the responsibility of the user of this standard to establish appropriate safety and health practices and determine the applicability of regulatory limitations prior to use.
信息:ICS:75.160.20 (Liquid fuels) CCS:E30 发布:2011 实施:
ASTM D7740-20 石油产品和润滑剂金属分析的原子吸收光谱法优化 校准和验证标准实践
简介:
信息:ICS:71.040.50 CCS: 发布:2020-07-01 实施:
ASTM D8127-2017 利用X射线荧光(XRF)对在用润滑剂进行颗粒物和元素耦合分析的标准试验方法
简介:5.1 It has been shown in many industries that separating information regarding small or dissolved elemental materials in the lubricant from suspended particulate is crucial. In many cases only an overall elemental analysis is provided, which may not capture significant wear or even machinery failure events. Such events are often accompanied by a sudden increase in the production of large particulate, which is suspended in and can be detected in the machineryx2019;s lubricant. This test method specifically targets such particulate, which has historically been difficult to quantify. Users of the technique include numerous military organizations, and maintainers of wind turbines, nuclear power facilities, and offshore rigs. 1.1x00a0;This automatic wear particle analysis2 test method for in-service lubricants describes using a combination of pore blockage particle counting and energy dispersive X-ray fluorescence (EDXRF) spectrometry for the quantitative determination of solid particle counts larger than four (4) micrometres, and elemental content of suspended particulate of iron (Fe) and copper (Cu) in such lubricants. 1.2x00a0;This test method provides for the determination of the elemental content of suspended particulate of Fe greater than 48201;x03bc;m in the range of 6 mg/kg to 223 mg/kg. Suspended particulate of copper greater than 48201;x03bc;m is determined in the range of 3.5 mg/kg to 92.4 mg/kg in the lubricant. Total particle count greater than 48201;x03bc;m is determined in the range of 118201;4958201;particles/mL greater than 48201;x03bc;m to 28201;1698201;5008201;particles/mL greater than 48201;x03bc;m in the lubricant. 1.3x00a0;This test method is applicable to all known in-service lubricants (API Groups I-V) at any stage of degradation. 1.4x00a0;This test method uses an empirical inter-element correction methodology. 1.5x00a0;The values stated in SI units are to be regarded as standard. No other units of measurement are included in this standard. 1.6x00a0;This standard does not purport to address all of the safety concerns, if any, associated with its use. It is the responsibility of the user of this standard to establish appropriate safety and health practices and determine the applicability of regulatory limitations prior to use. 1.7x00a0;This international standard was developed in accordance with internationally recognized principles on standardization established in the Decision on Principles for the Development of International Standards, Guides and Recommendations issued by the World Trade Organization Technical Barriers to Trade (TBT) Committee.
信息:ICS:75.100 CCS:E34 发布:2017 实施:
ASTM D7690-2011(2017) 采用分析铁谱技术对在用润滑剂中的颗粒进行显微特性描述的标准实施规程
简介:5.1x00a0;The objective of ferrography is to diagnose the operational condition of the machine sampled based on the quantity and type of particles observed in the oil. After break-in, normally running machines exhibit consistent particle concentration and particle types from sample to sample. An increase in particle concentration, accompanied by an increase in size and severity of particle types is indicative of initiation of a fault. This practice describes commonly found particles in in-service lubricants, but does not address methodology for quantification of particle concentration. 5.2x00a0;This practice is provided to promote improved and expanded use of ferrographic analysis with in-service lubricant analysis. It helps overcome some perceived complexity and resulting intimidation that effectively limits ferrographic analysis to the hands of a specialized and very limited number of practitioners. Standardized terminology and common reporting formats provide consistent interpretation and general understanding. 5.3x00a0;Without particulate debris analysis, in-service lubricant analysis results often fall short of concluding likely root cause or potential severity from analytical results because of missing information about the possible identification or extent of damaging mechanisms. 5.4x00a0;Ferrographic analysis, as described in this practice, provides additional particle identification capabilities beyond methods described in Guide D7684 for the following reasons: (1)x00a0;The ferrographic particle separation method is magnetic thus making it possible to readily distinguish between ferrous and nonferrous wear particles. (2)x00a0;Ferrography separates ferrous (magnetic) particles by size. (3)x00a0;Deposition is on a glass substrate so that particles may be examined using transmitted light as well as reflected light allowing particle types to be identified that cannot be identified when examination is done using only reflected light. (4)x00a0;Ferrograms may be heat treated providing important distinctions between ferrous alloy types (steel versus cast iron), further distinctions among various nonferrous alloys and distinctions between inorganic and organic particles. 5.5x00a0;Caution must be exercised when drawing conclusions from the particles found in a particular sample, especially if the sample being examined is the first from that type of machine. Some machines, during normal operation, generate wear particles that would be considered highly abnormal in other machines. For example, many gear boxes generate severe wear particles throughout their expected service life, whereas just a few severe wear particles from an aircraft gas turbine oil sample may be highly abnormal. Sound diagnostics require that a baseline, or typical wear particle signature, be established for each machine type under surveillance. 1.1x00a0;This practice covers the identification by optical microscopy of wear and contaminant particles commonly found in used lubricant and hydraulic oil samples that have been deposited on ferrograms. This practice relates to the identification of particles, but not to methods of determining particle concentration. 1.2x00a0;This pract......
信息:ICS:75.100 CCS:E34 发布:2011 实施:
ASTM D8321-20 基于光谱法预测石油产品、液体燃料和润滑剂特性的多元分析的开发和验证的标准实施规程测量
简介:
信息:ICS:75.080 CCS: 发布:2020-07-01 实施:
ASTM D7740-11(2016) 石油产品和润滑剂金属分析的原子吸收光谱法优化 校准和验证标准实践
简介:
信息:ICS:71.040.50 CCS: 发布:2016-04-01 实施:
KS B ISO 18436-4-2010 机器的工况监测和诊断.操作人员的认证和评估要求.第4部分:振动场润滑剂分析
简介:이 표준은 현장 윤활제 분석을 이용하여 기계의 상태 감시 및 진단 업무를 수행하는 요원의
信息:ICS:03.100.30 CCS:J04 发布:2010-12-22 实施:2010-12-22
ASTM D7260-20 用于石油产品和润滑剂元素分析的电感耦合等离子体原子发射光谱法(ICP-AES)的优化 校准和验证的标准实践
简介:
信息:ICS:75.080 CCS: 发布:2020-07-01 实施:
ASTM D4927-15 润滑剂和添加剂成分元素分析的标准试验方法&x2014;用波长色散X射线荧光光谱法测定钡、钙、磷、硫和锌
简介:
信息:ICS:75.100 CCS: 发布:2015-12-01 实施:
ASTM D7417-10 使用特殊的四部分集成测试仪(原子发射光谱 红外光谱 粘度和激光粒子计数器)分析使用中润滑剂的标准测试方法
简介:
信息:ICS:75.100 CCS: 发布:2010-10-01 实施:
ASTM D7578-20 石油产品和润滑剂元素分析校准要求的标准指南
简介:
信息:ICS:75.080 CCS: 发布:2020-05-01 实施:
ASTM D7416-09(2015) 使用特殊的五部分(介电介电常数、带开关磁场的时间分辨介电常数、激光粒子计数器、显微碎片分析和轨道粘度计)综合测试仪分析在用润滑剂的标准实施规程
简介:
信息:ICS:75.100 CCS: 发布:2015-06-01 实施:
ASTM D4927-10 润滑剂和添加剂组分元素分析的标准试验方法&8212;用波长色散X射线荧光光谱法测定钡、钙、磷、硫和锌
简介:
信息:ICS:75.100 CCS: 发布:2010-07-01 实施:
ASTM D4927-15(2020) 润滑剂和添加剂成分元素分析的标准试验方法&x2014;用波长色散X射线荧光光谱法测定钡、钙、磷、硫和锌
简介:
信息:ICS:75.100 CCS: 发布:2020-05-01 实施:
ASTM D7578-15 石油产品和润滑剂元素分析校准要求的标准指南
简介:
信息:ICS:75.080 CCS: 发布:2015-06-01 实施:
ASTM D7578-10 石油产品和润滑剂元素分析校准要求的标准指南
简介:
信息:ICS:75.080 CCS: 发布:2010-02-15 实施:
ASTM D7416-09(2020) 使用特殊的五部分(介电介电常数、带开关磁场的时间分辨介电常数、激光粒子计数器、显微碎片分析和轨道粘度计)综合测试仪分析在用润滑剂的标准实施规程
简介:
信息:ICS:75.100 CCS: 发布:2020-05-01 实施:
ASTM D4927-2015 润滑剂和添加剂元素分析的标准试验方法. 用波长色散X射线荧光光谱法测定钡, 钙, 磷, 硫和锌的含量
简介:4.1x00a0;Some oils are formulated with organo-metallic additives which act as detergents, antioxidants, antiwear agents, and so forth. Some of these additives contain one or more of these elements: barium, calcium, phosphorus, sulfur, and zinc. These test methods provide a means of determining the concentration of these elements which in turn provides an indication of the additive content of these oils. 4.2x00a0;Several additive elements and their compounds are added to the lubricating oils to give beneficial performance (see Table 2). 1.1x00a0;These test methods cover the determination of barium, calcium, phosphorus, sulfur, and zinc in unused lubricating oils at element concentration ranges shown in Table 1. The range can be extended to higher concentrations by dilution of sample specimens. Additives can also be determined after dilution. Two different methods are presented in these test methods. 1.2x00a0;Test Method A (Internal Standard Procedure)x2014;Internal standards are used to compensate for interelement effects of X-ray excitation and fluorescence (see Sections 8 through 13). 1.3x00a0;Test Method B (Mathematical Correction Procedure)x2014;The measured X-ray fluorescence intensity for a given element is mathematically corrected for potential interference from other elements present in the sample (see Sections 14 through 19). 1.4x00a0;The preferred concentration units are mass8201;% barium, calcium, phosphorus, sulfur, or zinc. 1.5x00a0;This standard does not purport to address all of the safety concerns, if any, associated with its use. It is the responsibility of the user of this standard to establish appropriate safety and health practices and determine the applicability of regulatory limitations prior to use.
信息:ICS:75.100 CCS: 发布:2015 实施:
ASTM D7578-10e1 石油产品和润滑剂元素分析校准要求的标准指南
简介:
信息:ICS:75.080 CCS: 发布:2010-02-15 实施:
ASTM D7260-19 用于石油产品和润滑剂元素分析的电感耦合等离子体原子发射光谱法(ICP-AES)的优化 校准和验证的标准实践
简介:
信息:ICS:75.080 CCS: 发布:2019-05-01 实施:
ASTM D4927-14 润滑剂和添加剂成分元素分析的标准试验方法—用波长色散X射线荧光光谱法测定钡、钙、磷、硫和锌
简介:
信息:ICS:75.100 CCS: 发布:2014-12-01 实施:
ASTM D7578-2010 石油产品和润滑剂元素分析的校准要求的标准指南
简介:Crude oil, petroleum, petroleum products, additives, biofuels, and lubricants are routinely analyzed for their elemental content such as chlorine, nitrogen, hydrogen, phosphorus, sulfur, and various metals using a variety of analytical techniques. Some of these methods require little to no method calibration; some others require only simple one step calibration; while others require elaborate calibration routine before the product is analyzed for its elemental content. Fairly often it can be shown that the round robin results by a co-operator are all biased with respect to those from other laboratories. Presumably, the failure to follow good laboratory practices and instructions in the test methods can be a causal factor of such errors. A further consequence is an unnecessarily large reproducibility estimate or the data being dropped from the study as an outlier. Another cause of such discrepancies could be different or inadequate calibration practice used in the laboratory. Most test methods spell out the calibration requirements but often do not quote the frequency required letting the laboratories use good laboratory practices for this task. Thus, uniform practice for instrument calibration would be beneficial in standardizing the test procedures and obtaining consistent results across the laboratories. Committee D02 has already issued standard practices for uniform sample preparation (D7455), standard operating procedures for ICP-AES (D7260) and XRF (D7343) as well as standard quality assurance protocol (D6792). This guide should be considered as a continuing effort on behalf of this subcommittee to achieve standardized practices in all parts of an analytical sequence.1.1 This guide covers different ways by which the test methods used for elemental analysis of petroleum product and lubricant samples are calibrated before the sample analysis. 1.2 Uniform practice for test method calibration is beneficial in standardizing the procedures, and obtaining consistent results across different laboratories. 1.3 This guide includes only the basic steps for generally encountered instrument types. Anything out of the ordinary may require special procedures. See individual test methods for instructions to handle such situations. 1.4 This guide is not a substitute for a thorough understanding of the actual test method to be used, caveats it contains, and additional instrument preparation that may be required. 1.5 The user should not expand the scope of the test methods to materials or concentrations outside the scope of the test methods being used. 1.6 This guide should also be applicable to sample preparation of non-petroleum based bio-fuels for elemental analysis. Work is underway on these aspects in Subcommittee D02.03. As more information becomes available, it will be added to this standard. 1.7 The values stated in SI units are to be regarded as standard. No other units of measurement are included in this standard. 1.8 This standard does not purport to address all of the safety concerns, if any, associated with its use. It is the responsibility of the user of this standard to establish appropriate safety and health practices and determine the applicability of regulatory limitations prior to use.
信息:ICS:75.100 (Lubricants, industrial oils and related pr CCS:E34 发布:2010 实施:
ASTM D7455-19 元素分析用石油和润滑剂产品样品制备的标准实施规程
简介:
信息:ICS:75.100 CCS: 发布:2019-05-01 实施:
ASTM D7455-14 元素分析用石油和润滑剂产品样品制备的标准实施规程
简介:
信息:ICS:75.100 CCS: 发布:2014-05-01 实施:
ASTM D7417-2010 使用特殊的四部分集成测试仪分析使用中的润滑剂的标准试验方法(原子发射光谱法,红外光谱学,粘度和激光微粒计数器)
简介:The integrated tester is primarily used to perform on-site analysis of in-service lubricants used in the automotive, highway trucking, mining, construction, off-road x201C;mining,x201D; marine, industrial, power generation, agriculture, and manufacturing industries. The immediate results of analysis of in-service lubricants are critical when performing proactive and preventative maintenance. On-site oil analysis, when used in conjunction with these programs, allows continuous system monitoring and contamination control potentially improving equipment x201C;up-timex201D; and equipment life.1.1 This test method covers the quantitative analysis of in-service lubricants using an automatic testing device that integrates these varied technologies: atomic emission spectroscopy, infrared spectroscopy, viscosity, and particle counting. 1.2 This is suited for in-service lubricating oils having viscosities in the range between ISO 10 and ISO 320 and properties in the ranges given in Tables 1 and 2. 1.3 This test method may be used to establish trends in wear and contamination of in-service lubricants and may not give equivalent numerical results to current ASTM test methods. 1.4 This test method is not intended for use with crude oil. 1.5 The values stated in SI units are to be regarded as standard. No other units of measurement are included in this standard. 1.6 This standard does not purport to address all of the safety concerns, if any, associated with its use. It is the responsibility of the user of this standard to establish appropriate safety and health practices and determine the applicability of regulatory limitations prior to use. (Specific hazard statements are given in Section 9 and 11.3.)
信息:ICS:75.100 CCS:E36 发布:2010 实施:
ASTM D7874-13(2018) 在用润滑剂试验中应用失效模式和影响分析(FMEA)的标准指南
简介:
信息:ICS:75.100 CCS: 发布:2018-12-01 实施:
ISO 18436-4:2014 机器的状态监测和诊断——人员资格鉴定和评估要求第4部分:现场润滑剂分析
简介:
信息:ICS:03.100.30 CCS: 发布:2014-02-03 实施:
ASTM D4927-2010 波长色散X射线荧光光谱法对润滑剂和钡、钙、磷、硫以及锌等添加组分急性元素分析的标准试验方法
简介:Some oils are formulated with organo-metallic additives which act as detergents, antioxidants, antiwear agents, and so forth. Some of these additives contain one or more of these elements: barium, calcium, phosphorus, sulfur, and zinc. These test methods provide a means of determining the concentration of these elements which in turn provides an indication of the additive content of these oils.1.1 These test methods cover the determination of barium, calcium, phosphorus, sulfur, and zinc in unused lubricating oils at element concentration ranges shown in Table 1. The range can be extended to higher concentrations by dilution of sample specimens. Additives can also be determined after dilution. Two different methods are presented in these test methods. 1.2 Test Method A (Internal Standard Procedure)8212;Internal standards are used to compensate for interelement effects of X-ray excitation and fluorescence (see Sections 8 through 13). 1.3 Test Method B (Mathematical Correction Procedure)8212;The measured X-ray fluorescence intensity for a given element is mathematically corrected for potential interference from other elements present in the sample (see Sections 14 through 19). 1.4 The preferred concentration units are mass % barium, calcium, phosphorus, sulfur, or zinc. 1.5 This standard does not purport to address all of the safety concerns, if any, associated with its use. It is the responsibility of the user of this standard to establish appropriate safety and health practices and determine the applicability of regulatory limitations prior to use.
信息:ICS:75.100 (Lubricants, industrial oils and related pr CCS:E34 发布:2010 实施:
ASTM D7578-18 石油产品和润滑剂元素分析校准要求的标准指南
简介:
信息:ICS:75.080 CCS: 发布:2018-06-01 实施:
DIN 51820-2013 润滑剂检测.采用红外光谱测定法对润滑脂的分析.红外光谱的记录和解释
简介:
信息:ICS:75.100 CCS:E34 发布:2013-12 实施:
ASTM D7624-2010 用傅里叶变换红外(FT-IR)光谱测定法通过趋势分析对使用中的石油和烃基润滑剂中硝化作用的状态进行监控的标准试验方法
简介:There is a wide variety of nitration compounds that may be produced and accumulate when oils react with gaseous nitrates formed during the engine combustion process. These nitration products may increase the viscosity, acidity and insolubles in the oil, which may lead to ring sticking and filter plugging. Monitoring of nitration products is therefore an important parameter in determining overall machinery health and should be considered in conjunction with data from other tests such as atomic emission (AE) and atomic absorption (AA) spectroscopy for wear metal analysis (Test Method D5185), physical property tests (Test Methods D445, D6304, and D2896), and other FT-IR oil analysis methods for oxidation (Test Method ), sulfate by-products (Test Method D7415), additive depletion (Test Method D7412), and breakdown products and external contaminants (Practice E2412), which also assess elements of the oilx2019;s condition. (1-6)1.1 This test method covers monitoring nitration in gasoline and natural gas engine oils as well as in other types of lubricants where nitration by-products may form due to the combustion process or other routes of formation of nitration compounds. 1.2 This test method uses FT-IR spectroscopy for monitoring build-up of nitration by-products in in-service petroleum and hydrocarbon-based lubricants as a result of normal machinery operation. Nitration levels in gasoline and natural gas engine oils rise as combustion by-products react with the oil as a result of exhaust gas recirculation or a blow-by. This test method is designed as a fast, simple spectroscopic check for monitoring of nitration in in-service petroleum and hydrocarbon-based lubricants with the objective of helping diagnose the operational condition of the machine based on measuring the level of nitration in the oil. 1.3 Acquisition of FT-IR spectral data for measuring nitration in in-service oil and lubricant samples is described in Practice D7418. In this test method, measurement and data interpretation parameters for nitration using both direct trend analysis and differential (spectral subtraction) trend analysis are presented. 1.4 This test method is based on trending of spectral changes associated with nitration in in-service petroleum and hydrocarbon-based lubricants. For direct trend analysis, values are recorded directly from absorption spectra and reported in units of 100*absorbance per 0.1 mm pathlength (or equivalently absorbance units per centimetre). For differential trend analysis, values are recorded from the differential spectra (spectrum obtained by subtraction of the spectrum of the reference oil from that of the in-service oil) and reported in units of 100*absorbance per 0.1 mm pathlength (or equivalently absorbance units per centimetre). Warnings or alarm limits can be set on the basis of a fixed maximum value for a single measurement or, alternatively, can be based on a rate of change of the response measured. (1) In either case, such maintenance action limits should be determined through statistical analysis, h......
信息:ICS:75.160.20 CCS:E30 发布:2010 实施:
ASTM D7343-18 用于石油产品和润滑剂元素分析的X射线荧光光谱法优化 样品处理 校准和验证的标准操作规程
简介:
信息:ICS:71.040.50 CCS: 发布:2018-06-01 实施:
ASTM D7874-13 在用润滑剂试验中应用失效模式和影响分析(FMEA)的标准指南
简介:
信息:ICS:75.100 CCS: 发布:2013-10-01 实施:
ASTM D7578-2010e1 石油产品和润滑剂元素分析所需的校准要求的标准指南
简介:Crude oil, petroleum, petroleum products, additives, biofuels, and lubricants are routinely analyzed for their elemental content such as chlorine, nitrogen, hydrogen, phosphorus, sulfur, and various metals using a variety of analytical techniques. Some of these methods require little to no method calibration; some others require only simple one step calibration; while others require elaborate calibration routine before the product is analyzed for its elemental content. Fairly often it can be shown that the round robin results by a co-operator are all biased with respect to those from other laboratories. Presumably, the failure to follow good laboratory practices and instructions in the test methods can be a causal factor of such errors. A further consequence is an unnecessarily large reproducibility estimate or the data being dropped from the study as an outlier. Another cause of such discrepancies could be different or inadequate calibration practice used in the laboratory. Most test methods spell out the calibration requirements but often do not quote the frequency required letting the laboratories use good laboratory practices for this task. Thus, uniform practice for instrument calibration would be beneficial in standardizing the test procedures and obtaining consistent results across the laboratories. Committee D02 has already issued standard practices for uniform sample preparation (D7455), standard operating procedures for ICP-AES (D7260) and XRF (D7343) as well as standard quality assurance protocol (D6792). This guide should be considered as a continuing effort on behalf of this subcommittee to achieve standardized practices in all parts of an analytical sequence.1.1 This guide covers different ways by which the test methods used for elemental analysis of petroleum product and lubricant samples are calibrated before the sample analysis. 1.2 Uniform practice for test method calibration is beneficial in standardizing the procedures, and obtaining consistent results across different laboratories. 1.3 This guide includes only the basic steps for generally encountered instrument types. Anything out of the ordinary may require special procedures. See individual test methods for instructions to handle such situations. 1.4 This guide is not a substitute for a thorough understanding of the actual test method to be used, caveats it contains, and additional instrument preparation that may be required. 1.5 The user should not expand the scope of the test methods to materials or concentrations outside the scope of the test methods being used. 1.6 This guide should also be applicable to sample preparation of non-petroleum based bio-fuels for elemental analysis. Work is underway on these aspects in Subcommittee D02.03. As more information becomes available, it will be added to this standard. 1.7 The values stated in SI units are to be regarded as standard. No other units of measurement are included in this standard. 1.8 This standard does not purport to address all of the safety concerns, if any, associated with its use. It is the responsibility of the user of this standard to establish appropriate safety and health practices and determine the applicability of regulatory limitations prior to use.
信息:ICS:75.100 (Lubricants, industrial oils and related pr CCS:E34 发布:2010 实施:
ASTM D7844-18 使用傅里叶变换红外(FT-IR)光谱法通过趋势分析对在线润滑剂中的烟灰进行状态监测的标准测试方法
简介:
信息:ICS:75.160.20 CCS: 发布:2018-01-01 实施:
ASTM D7874-2013 在用润滑剂试验失效模式与效果分析(FMEA)应用标准指南
简介:5.1x00a0;This guide is intended as a guideline for fluid analysis programs and serves as an initial justification for selecting fluid tests and sampling frequencies. Plant operating experience along with the review and benchmarking of similar applications is required to ensure that lessons learned are implemented. 5.2x00a0;Selection of proper fluid tests for assessing in-service component condition may have both safety and economic implications. Some failure modes may cause component disintegration, increasing the safety hazard. Thus, any fluid test that can predict such conditions should be included in the condition-monitoring program. Conversely, to maintain a sustainable and successful fluid-monitoring program, the scope of the fluid tests and their frequency should be carefully balanced between the associated risks versus expected program cost savings and benefits. 5.3x00a0;The failure modes monitored may be similar from one application to the next, but the risk and consequences of failure may differ. 5.4x00a0;This analysis can be used to determine which in-service lubricant analysis tests would be of highest value and which would be ineffective for the failure modes of interest. This information can also be used to determine the best monitoring strategy for a suite of failure modes and how often assessment is needed to manage the risk of failure. 1.1x00a0;This guide describes a methodology to select tests to be used for in-service lubricant analysis. The selection of fluid tests for monitoring failure mode progression in industrial applications applies the principles of failure mode and effect analysis (FMEA). 1.2x00a0;Although typical FMEA addresses all possible product failure modes, the focus of this guide is not intended to address failures that have a very high probability of unsafe operation as these should immediately be addressed by other means. 1.3x00a0;This guide is limited to components selected for condition-monitoring programs by providing a methodology to choose fluid tests associated with specific failure modes for the purpose of identifying their earliest developing stage and monitoring fault progression. The scope of this guide is also focused on those failure modes and their consequences that can effectively be detected and monitored by fluid analysis techniques. 1.4x00a0;This guide pertains to a process to be used to ensure an appropriate amount of condition monitoring is performed with the objective of improving equipment reliability, reducing maintenance costs, and enhancing fluid analysis monitoring of industrial machinery. This guide can also be used to select the monitoring frequencies needed to make the failure determinations and provide an assessment of the strengths and weaknesses of a current condition-monitoring program. 1.5x00a0;This guide does not eliminate the programmatic requirements for appropriate assembly, operational, and maintenance practices. 1.6x00a0;This standard does not purport to address all of the safety concerns, if any, associated with its use. It is the responsibility of the user of this standard to establish appropriate safety and health practices and determine the applicability of regulatory limitations prior to use.
信息:ICS:75.100 (Lubricants, industrial oils and related pr CCS:E34 发布:2013 实施:
ASTM E2412-2010 傅里叶变换红外线(FT-IR)光谱测定法通过趋势分析监测使用过的润滑剂状态的标准实施规程
简介:Periodic sampling and analysis of lubricants have long been used as a means to determine overall machinery health. Atomic emission (AE) and atomic absorption (AA) spectroscopy are often employed for wear metal analysis (for example, Test Method D5185). A number of physical property tests complement wear metal analysis and are used to provide information on lubricant condition (for example, Test Methods D445, D2896, and D6304). Molecular analysis of lubricants and hydraulic fluids by FT-IR spectroscopy produces direct information on molecular species of interest, including additives, fluid breakdown products and external contaminants, and thus complements wear metal and other analyses used in a condition monitoring program (1,3-7).1.1 This practice covers the use of FT-IR in monitoring additive depletion, contaminant buildup and base stock degradation in machinery lubricants, hydraulic fluids and other fluids used in normal machinery operation. Contaminants monitored include water, soot, ethylene glycol, fuels and incorrect oil. Oxidation, nitration and sulfonation of base stocks are monitored as evidence of degradation. The objective of this monitoring activity is to diagnose the operational condition of the machine based on fault conditions observed in the oil. Measurement and data interpretation parameters are presented to allow operators of different FT-IR spectrometers to compare results by employing the same techniques. 1.2 This practice is based on trending and distribution response analysis from mid-infrared absorption measurements. While calibration to generate physical concentration units may be possible, it is unnecessary or impractical in many cases. Warning or alarm limits (the point where maintenance action on a machine being monitored is recommended or required) can be determined through statistical analysis, history of the same or similar equipment, round robin tests or other methods in conjunction with correlation to equipment performance. These warning or alarm limits can be a fixed maximum or minimum value for comparison to a single measurement or can also be based on a rate of change of the response measured (1). This practice describes distributions but does not preclude using rate-of-change warnings and alarms. Note 18212;It is not the intent of this practice to establish or recommend normal, cautionary, warning or alert limits for any machinery. Such limits should be established in conjunction with advice and guidance from the machinery manufacturer and maintenance group. 1.3 Spectra and distribution profiles presented herein are for illustrative purposes only and are not to be construed as representing or establishing lubricant or machinery guidelines. 1.4 This practice is designed as a fast, simple spectroscopic check for condition monitoring of in-service lubricants and can be used to assist in the determination of general machinery health through measurement of properties observable in the mid-infrared spectrum such as water, oil oxidation, and others as noted in 1.1. The infrared data generated by this practice is typically used in conjunction with other testing methods. For example, infrared spectroscopy cannot determine wear metal levels or any other type of elemental analysis. The practice as presented is not intended for the prediction of lubricant physical properties (for example, viscosity, total base number, total acid number, etc.). This prac......
信息:ICS:75.100 CCS:E34 发布:2010 实施:
我们的实力
部分实验仪器




合作客户
注意:因业务调整,暂不接受个人委托测试望见谅。