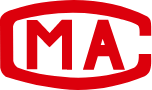



应变疲劳检测标准相关标准参考信息
GB/T 41154-2021 金属材料 多轴疲劳试验 轴向-扭转应变控制热机械疲劳试验方法
简介:
信息:ICS:77.040.10 CCS:H22 发布:2021-12-31 00:00:00.0 实施:2022-07-01 00:00:00.0
ASTM E2207-15 用薄壁管状样品进行应变控制轴向扭转疲劳试验的标准实践
简介:
信息:ICS:19.060 CCS: 发布:2015-05-01 实施:
KS B ISO 12106-2004(2019) 金属材料疲劳试验轴向应变控制法
简介:
信息:ICS:77.040.10 CCS: 发布:2004-12-24 实施:
GB/T 40410-2021 金属材料 多轴疲劳试验 轴向-扭转应变控制方法
简介:
信息:ICS:77.040.10 CCS:H22 发布:2021-08-20 00:00:00.0 实施:2022-03-01 00:00:00.0
ASTM E1949-03(2014) 金属接合电阻应变片的环境温度疲劳寿命的标准测试方法
简介:
信息:ICS:19.060 CCS: 发布:2014-04-15 实施:
KS B ISO 12106-2004 金属材料.疲劳试验.轴向应变控制法
简介:이 규격은 단축 하중 시험편을 시험하는 방법을 규정하는 것으로 이 때의 조건은 일정한 주기
信息:ICS:77.040.10 CCS:H22 发布:2004-12-24 实施:2004-12-24
GB/T 26077-2021 金属材料 疲劳试验 轴向应变控制方法
简介:
信息:ICS:77.040.10 CCS:H22 发布:2021-04-30 00:00:00.0 实施:2021-11-01 00:00:00.0
ASTM E606/E606M-12 应变控制疲劳试验的标准试验方法
简介:
信息:ICS:77.040.10 CCS: 发布:2012-06-01 实施:
KS B ISO 12106-2004 金属材料.疲劳试验.轴向应变控制法
简介:이 규격은 단축 하중 시험편을 시험하는 방법을 규정하는 것으로 이 때의 조건은 일정한 주기
信息:ICS:77.040.10 CCS:H22 发布:2004-12-24 实施:2004-12-24
GB/T 35465.2-2017 聚合物基复合材料疲劳性能测试方法 第2部分:线性或线性化应力寿命(S-N)和应变寿命(ε-N)疲劳数据的统计分析
简介:
信息:ICS:83.120 CCS:Q23 发布:2017-12-29 00:00:00.0 实施:2018-11-01 00:00:00.0
ASTM E606/E606M-2012 应变控制疲劳试验的标准试验方法
简介:Strain-controlled fatigue is a phenomenon that is influenced by the same variables that influence force-controlled fatigue. The nature of strain-controlled fatigue imposes distinctive requirements on fatigue testing methods. In particular, cyclic total strain should be measured and cyclic plastic strain should be determined. Furthermore, either of these strains typically is used to establish cyclic limits; total strain usually is controlled throughout the cycle. The uniqueness of this test method and the results it yields are the determination of cyclic stresses and strains at any time during the tests. Differences in strain histories other than constant-amplitude alter fatigue life as compared with the constant amplitude results (for example, periodic overstrains and block or spectrum histories). Likewise, the presence of nonzero mean strains and varying environmental conditions may alter fatigue life as compared with the constant-amplitude, fully reversed fatigue tests. Care must be exercised in analyzing and interpreting data for such cases. In the case of variable amplitude or spectrum strain histories, cycle counting can be performed with Practice E1049 . Strain-controlled fatigue can be an important consideration in the design of industrial products. It is important for situations in which components or portions of components undergo either mechanically or thermally induced cyclic plastic strains that cause failure within relatively few (that is, approximately x003C;105) cycles. Information obtained from strain-controlled fatigue testing may be an important element in the establishment of design criteria to protect against component failure by fatigue. Strain-controlled fatigue test results are useful in the areas of mechanical design as well as materials research and development, process and quality control, product performance, and failure analysis. Results of a strain-controlled fatigue test program may be used in the formulation of empirical relationships between the cyclic variables of stress, total strain, plastic strain, and fatigue life. They are commonly used in data correlations such as curves of cyclic stress or strain versus life and cyclic stress versus cyclic plastic strain obtained from hysteresis loops at some fraction (often half) of material life. Examination of the cyclic stressx2013;strain curve and its comparison with monotonic stressx2013;strain curves gives useful information regarding the cyclic stability of a material, for example, whether the values of hardness, yield strength, ultimate strength, strain-hardening exponent, and strength coefficient will increase, decrease, or remain unchanged (that is, whether a material will harden, soften, or be stable) because of cyclic plastic straining (1). The presence of time-dependent inelastic strains during elevated temperature testing provides the opportunity to study the effects of these strains on fatigue life and on the cyclic stress-strain response of the material. Information about strain rate effects, relaxation behavior, and creep also may be available from these tests. Results of the uniaxial tests on specimens of simple geometry can be applied to the design of components with notches or other complex shapes, provided that the strains can be determined and multiaxial states of stress or strain and their gradients are correctly correlated with the uniaxial strain data.1.1 This test method covers the determination of fatigue properties of nominally homogeneous materials by the use of test specimens subjected to uniaxial forces. It is intended as a guide for fatigue testing performed in support of such activities as materials research and development, mechanical design, pro......
信息:ICS:77.040.10 (Mechanical testing of metals) CCS: 发布:2012 实施:
SAE J2409-2004 应变寿命疲劳数据交换文档格式
简介:SAE format for a SIMPLE strain-life fatigue data exchange file format. The object of this SAE Standard is to provide a simple common way to exchange strain-life fatigue data collected from ASTM E 606 axial fatigue test data.
信息:ICS:19.060;35.240.50 CCS:L67 发布:2004-11-04 实施:
GB/T 33812-2017 金属材料 疲劳试验 应变控制热机械疲劳试验方法
简介:
信息:ICS:77.040.10 CCS:H22 发布:2017-05-31 00:00:00.0 实施:2017-12-01 00:00:00.0
ISO 12111:2011 金属材料——疲劳试验——应变控制热机械疲劳试验方法
简介:
信息:ICS:77.040.10 CCS: 发布:2011-08-10 实施:
ASTM E606-04e1 应变控制疲劳试验的标准实施规程
简介:
信息:ICS:77.040.10 CCS: 发布:2004-10-01 实施:
GB/T 1687.3-2016 硫化橡胶 在屈挠试验中温升和耐疲劳性能的测定 第3部分:压缩屈挠试验(恒应变型)
简介:
信息:ICS:83.060 CCS:G40 发布:2016-12-13 00:00:00.0 实施:2017-07-01 00:00:00.0
ISO 12111-2011 金属材料.疲劳试验.受控应变热机械疲劳试验方法
简介:
信息:ICS:77.040.10 CCS:H22 发布:2011-08 实施:
ASTM E606-04 应变控制疲劳试验的标准实施规程
简介:
信息:ICS:77.040.10 CCS: 发布:2004-10-01 实施:
GB/T 26077-2010 金属材料.疲劳试验.轴向应变控制方法
简介:本标准规定了金属材料轴向应变控制疲劳试验的定义、符号、试验设备、试验程序、数据处理和试验报告。本标准适用于在恒温横幅条件下应变控制且应变比R=-1的单轴加载式样。本标准也可用于指导在其他条件下进行的疲劳试验。
信息:ICS:77.040.10 CCS:H22 发布:2011-01-10 实施:2011-10-01
ASTM E739-10 线性或线性化应力寿命(
简介:
信息:ICS:19.060 CCS: 发布:2010-11-01 实施:
SAE J2649-2004 应变寿命超载疲劳数据文档格式
简介:SAE data file format for exchanging controlled periodic overload data. The object of this SAE Standard is to provide a simple, common methodology for exchanging the data from periodic overload fatigue tests. These tests consist of a single large fatigue cycle followed by a larger number of smaller cycles. The overloads are fully reversed fatigue cycles while the smaller cycles share a common mean and amplitude.
信息:ICS:43.020;35.060 CCS:T04 发布:2004-08-31 实施:
ISO 4666-3-2022 硫化橡胶.挠曲试验中温升和耐疲劳性的测定.第3部分:压缩挠曲试验(恒定应变型)
简介:
信息:ICS:83.060 CCS: 发布:2022-12-21 实施:
KS M ISO 24999-2010(2021) 软质泡沫聚合材料-用恒定应变法测定疲劳
简介:
信息:ICS:83.100 CCS: 发布:2010-06-15 实施:
ASTM E606-92(2004)e1 应变控制疲劳试验的标准实施规程
简介:
信息:ICS:77.040.10 CCS: 发布:2004-07-01 实施:
T/CSTM 00790.3-2022 汽车用薄钢板 第3部分:轴向应变控制疲劳试验方法
简介:本文件规定了室温下汽车用薄钢板试样(没有引入应力集中)轴向应变控制疲劳试验的术语和定义、符号和说明、设备、试样、试验程序、数据处理和试验报告。本文件适用于厚度不大于3.0mm(试样最小厚度0.5mm)的汽车用薄钢板(不包括缺口试样)在恒幅条件下应变控制且应变比Re=-1的轴向加载试验。指定在其他应变比Re下进行试验也可参照执行。
信息:ICS:77.040.10 CCS:M745 发布:2022-11-23 实施:2022-11-23
ASTM E2368-10 应变控制热机械疲劳试验的标准操作规程
简介:
信息:ICS:19.060 CCS: 发布:2010-05-01 实施:
ASTM E2368-04e1 应变控制热机械疲劳试验的标准操作规程
简介:
信息:ICS:19.060 CCS: 发布:2004-05-01 实施:
ASTM E606/E606M-21 应变控制疲劳试验的标准试验方法
简介:
信息:ICS:77.040.10 CCS: 发布:2021-06-01 实施:
ASTM E739-2010(2015) 线性或者线性化应力寿命 (S-N) 和应变寿命 (N) 疲劳数据的统计分析的标准实施规程
简介:4.1x00a0;Materials scientists and engineers are making increased use of statistical analyses in interpreting S-N and x03b5;-N fatigue data. Statistical analysis applies when the given data can be reasonably assumed to be a random sample of (or representation of) some specific defined population or universe of material of interest (under specific test conditions), and it is desired either to characterize the material or to predict the performance of future random samples of the material (under similar test conditions), or both. 1.1x00a0;This practice covers only S-N and x03b5;-N relationships that may be reasonably approximated by a straight line (on appropriate coordinates) for a specific interval of stress or strain. It presents elementary procedures that presently reflect good practice in modeling and analysis. However, because the actual S-N or x03b5;-N relationship is approximated by a straight line only within a specific interval of stress or strain, and because the actual fatigue life distribution is unknown, it is not recommended that (a) the S-N or x03b5;-N curve be extrapolated outside the interval of testing, or (b) the fatigue life at a specific stress or strain amplitude be estimated below approximately the fifth percentile (P x2243; 0.05). As alternative fatigue models and statistical analyses are continually being developed, later revisions of this practice may subsequently present analyses that permit more complete interpretation of S-N and x03b5;-N data.
信息:ICS:19.060 CCS: 发布:2010 实施:
ASTM E739-91(2004) 线性或线性化应力寿命(S-N)和应变寿命(&949- N)疲劳数据
简介:
信息:ICS: CCS: 发布:2004-05-01 实施:
ASTM E2207-15(2021) 薄壁管状试样应变控制轴向扭转疲劳试验的标准实施规程
简介:
信息:ICS:19.060 CCS: 发布:2021-06-01 实施:
ASTM E2368-2010 应变控制式热机械疲劳试验的标准实施规程
简介:In the utilization of structural materials in elevated temperature environments, components that are susceptible to fatigue damage may experience some form of simultaneously varying thermal and mechanical forces throughout a given cycle. These conditions are often of critical concern because they combine temperature dependent and cycle dependent (fatigue) damage mechanisms with varying severity relating to the phase relationship between cyclic temperature and cyclic mechanical strain. Such effects can be found to influence the evolution of microstructure, micromechanisms of degradation, and a variety of other phenomenological processes that ultimately affect cyclic life. The strain-controlled thermomechanical fatigue test is often used to investigate the effects of simultaneously varying thermal and mechanical loadings under idealized conditions, where cyclic theoretically uniform temperature and strain fields are externally imposed and controlled throughout the gage section of the specimen.1.1 This practice covers the determination of thermomechanical fatigue (TMF) properties of materials under uniaxially loaded strain-controlled conditions. A x201C;thermomechanicalx201D; fatigue cycle is here defined as a condition where uniform temperature and strain fields over the specimen gage section are simultaneously varied and independently controlled. This practice is intended to address TMF testing performed in support of such activities as materials research and development, mechanical design, process and quality control, product performance, and failure analysis. While this practice is specific to strain-controlled testing, many sections will provide useful information for force-controlled or stress-controlled TMF testing. 1.2 This practice allows for any maximum and minimum values of temperature and mechanical strain, and temperature-mechanical strain phasing, with the restriction being that such parameters remain cyclically constant throughout the duration of the test. No restrictions are placed on environmental factors such as pressure, humidity, environmental medium, and others, provided that they are controlled throughout the test, do not cause loss of or change in specimen dimensions in time, and are detailed in the data report. 1.3 The use of this practice is limited to specimens and does not cover testing of full-scale components, structures, or consumer products. 1.4 The values stated in SI units are to be regarded as standard. No other units of measurement are included in this standard.
信息:ICS:19.060 CCS:A40 发布:2010 实施:
ASTM E2368-04 应变控制热机械疲劳试验的标准操作规程
简介:
信息:ICS:19.060 CCS: 发布:2004-05-01 实施:
ASTM E1949-21 金属接合电阻应变片的环境温度疲劳寿命的标准测试方法
简介:
信息:ICS:19.060 CCS: 发布:2021-02-01 实施:
ASTM E2368-2010(2017) 应变控制式热机械疲劳试验的标准实施规程
简介:4.1x00a0;In the utilization of structural materials in elevated temperature environments, components that are susceptible to fatigue damage may experience some form of simultaneously varying thermal and mechanical forces throughout a given cycle. These conditions are often of critical concern because they combine temperature dependent and cycle dependent (fatigue) damage mechanisms with varying severity relating to the phase relationship between cyclic temperature and cyclic mechanical strain. Such effects can be found to influence the evolution of microstructure, micromechanisms of degradation, and a variety of other phenomenological processes that ultimately affect cyclic life. The strain-controlled thermomechanical fatigue test is often used to investigate the effects of simultaneously varying thermal and mechanical loadings under idealized conditions, where cyclic theoretically uniform temperature and strain fields are externally imposed and controlled throughout the gage section of the specimen. 1.1x00a0;This practice covers the determination of thermomechanical fatigue (TMF) properties of materials under uniaxially loaded strain-controlled conditions. A x201c;thermomechanicalx201d; fatigue cycle is here defined as a condition where uniform temperature and strain fields over the specimen gage section are simultaneously varied and independently controlled. This practice is intended to address TMF testing performed in support of such activities as materials research and development, mechanical design, process and quality control, product performance, and failure analysis. While this practice is specific to strain-controlled testing, many sections will provide useful information for force-controlled or stress-controlled TMF testing. 1.2x00a0;This practice allows for any maximum and minimum values of temperature and mechanical strain, and temperature-mechanical strain phasing, with the restriction being that such parameters remain cyclically constant throughout the duration of the test. No restrictions are placed on environmental factors such as pressure, humidity, environmental medium, and others, provided that they are controlled throughout the test, do not cause loss of or change in specimen dimensions in time, and are detailed in the data report. 1.3x00a0;The use of this practice is limited to specimens and does not cover testing of full-scale components, structures, or consumer products. 1.4x00a0;The values stated in SI units are to be regarded as standard. No other units of measurement are included in this standard. 1.5x00a0;This international standard was developed in accordance with internationally recognized principles on standardization established in the Decision on Principles for the Development of International Standards, Guides and Recommendations issued by the World Trade Organization Technical Barriers to Trade (TBT) Committee.
信息:ICS:19.060 CCS:A40 发布:2010 实施:
ASTM E606-2004 应变控制疲劳试验的标准实施规程
简介:1.1 This practice covers the determination of fatigue properties of nominally homogeneous materials by the use of test specimens subjected to uniaxial forces. It is intended as a guide for fatigue testing performed in support of such activities as materials research and development, mechanical design, process and quality control, product performance, and failure analysis. While this practice is intended primarily for strain-controlled fatigue testing, some sections may provide useful information for force-controlled or stress-controlled testing.1.2 The use of this practice is limited to specimens and does not cover testing of full-scale components, structures, or consumer products.1.3 This practice is applicable to temperatures and strain rates for which the magnitudes of time-dependent inelastic strains are on the same order or less than the magnitudes of time-independent inelastic strains. No restrictions are placed on environmental factors such as temperature, pressure, humidity, medium, and others, provided they are controlled throughout the test, do not cause loss of or change in dimension with time, and are detailed in the data report. Note 18212;The term inelastic is used herein to refer to all nonelastic strains. The term plastic is used herein to refer only to the time-independent (that is, noncreep) component of inelastic strain. To truly determine a time-independent strain the force would have to be applied instantaneously, which is not possible. A useful engineering estimate of time-independent strain can be obtained when the strain rate exceeds some value. For example, a strain rate of 1 10 3 sec1 is often used for this purpose. This value should increase with increasing test temperature.1.4 This practice is restricted to the testing of uniform gage section test specimens subjected to axial forces as shown in (a). Testing is limited to strain-controlled cycling. The practice may be applied to hourglass specimens, see (b), but the user is cautioned about uncertainties in data analysis and interpretation. Testing is done primarily under constant amplitude cycling and may contain interspersed hold times at repeated intervals. The practice may be adapted to guide testing for more general cases where strain or temperature may vary according to application specific histories. Data analysis may not follow this practice in such cases.
信息:ICS:77.040.10 (Mechanical testing of metals) CCS:H22 发布:2004 实施:
ASTM E606/E606M-19 应变控制疲劳试验的标准试验方法
简介:
信息:ICS:77.040.10 CCS: 发布:2019-11-01 实施:
ASTM E739-2010 线性或线性化应力寿命(
简介:Materials scientists and engineers are making increased use of statistical analyses in interpreting S-N and x03B5;-N fatigue data. Statistical analysis applies when the given data can be reasonably assumed to be a random sample of (or representation of) some specific defined population or universe of material of interest (under specific test conditions), and it is desired either to characterize the material or to predict the performance of future random samples of the material (under similar test conditions), or both. 1.1 This practice covers only S-N and x03B5;-N relationships that may be reasonably approximated by a straight line (on appropriate coordinates) for a specific interval of stress or strain. It presents elementary procedures that presently reflect good practice in modeling and analysis. However, because the actual S-N or x03B5;-N relationship is approximated by a straight line only within a specific interval of stress or strain, and because the actual fatigue life distribution is unknown, it is not recommended that (a) the S-N or x03B5;-N curve be extrapolated outside the interval of testing, or (b) the fatigue life at a specific stress or strain amplitude be estimated below approximately the fifth percentile (P x2243; 0.05). As alternative fatigue models and statistical analyses are continually being developed, later revisions of this practice may subsequently present analyses that permit more complete interpretation of S-N and x03B5;-N data.
信息:ICS:19.060 CCS:H22 发布:2010 实施:
ASTM E606-2004e1 应变控制疲劳试验的标准实施规程
简介:1.1 This practice covers the determination of fatigue properties of nominally homogeneous materials by the use of test specimens subjected to uniaxial forces. It is intended as a guide for fatigue testing performed in support of such activities as materials research and development, mechanical design, process and quality control, product performance, and failure analysis. While this practice is intended primarily for strain-controlled fatigue testing, some sections may provide useful information for force-controlled or stress-controlled testing.1.2 The use of this practice is limited to specimens and does not cover testing of full-scale components, structures, or consumer products.1.3 This practice is applicable to temperatures and strain rates for which the magnitudes of time-dependent inelastic strains are on the same order or less than the magnitudes of time-independent inelastic strains. No restrictions are placed on environmental factors such as temperature, pressure, humidity, medium, and others, provided they are controlled throughout the test, do not cause loss of or change in dimension with time, and are detailed in the data report. Note 18212;The term inelastic is used herein to refer to all nonelastic strains. The term plastic is used herein to refer only to the time-independent (that is, noncreep) component of inelastic strain. To truly determine a time-independent strain the force would have to be applied instantaneously, which is not possible. A useful engineering estimate of time-independent strain can be obtained when the strain rate exceeds some value. For example, a strain rate of 1 10 3 sec1 is often used for this purpose. This value should increase with increasing test temperature.1.4 This practice is restricted to the testing of uniform gage section test specimens subjected to axial forces as shown in Fig. 1(a). Testing is limited to strain-controlled cycling. The practice may be applied to hourglass specimens, see Fig. 1(b), but the user is cautioned about uncertainties in data analysis and interpretation. Testing is done primarily under constant amplitude cycling and may contain interspersed hold times at repeated intervals. The practice may be adapted to guide testing for more general cases where strain or temperature may vary according to application specific histories. Data analysis may not follow this practice in such cases.
信息:ICS:77.040.10 (Mechanical testing of metals) CCS:H22 发布:2004 实施:
ASTM E606/E606M-19e1 应变控制疲劳试验的标准试验方法
简介:
信息:ICS:77.040.10 CCS: 发布:2019-11-01 实施:
ASTM E1949-03(2009) 金属接合电阻应变片的环境温度疲劳寿命的标准测试方法
简介:
信息:ICS:19.060 CCS: 发布:2009-04-01 实施:
ASTM E2368-2004 应变控制热力疲劳试验的标准规程
简介:1.1 This practice covers the determination of thermomechanical fatigue (TMF) properties of materials under uniaxially loaded strain-controlled conditions. A "thermomechanical" fatigue cycle is here defined as a condition where uniform temperature and strain fields over the specimen gage section are simultaneously varied and independently controlled. This practice is intended to address TMF testing performed in support of such activities as materials research and development, mechanical design, process and quality control, product performance, and failure analysis. While this practice is specific to strain-controlled testing, many sections will provide useful information for force-controlled or stress-controlled TMF testing.1.2 This practice allows for any maximum and minimum values of temperature and mechanical strain, and temperature-mechanical strain phasing, with the restriction being that such parameters remain cyclically constant throughout the duration of the test. No restrictions are placed on environmental factors such as pressure, humidity, environmental medium, and others, provided that they are controlled throughout the test, do not cause loss of or change in specimen dimensions in time, and are detailed in the data report.1.3 The use of this practice is limited to specimens and does not cover testing of full-scale components, structures, or consumer products.
信息:ICS:19.060 (Mechanical testing) CCS:A40 发布:2004 实施:
JIS K6270-2018 硫化橡胶或热塑性塑料.张力疲劳测定(恒定应变法)
简介:
信息:ICS:83.060 CCS:G34 发布:2018-06-20 实施:
ASTM E1949-03(2014)e1 金属接合电阻应变片的环境温度疲劳寿命的标准测试方法
简介:
信息:ICS:19.060 CCS: 发布:2009-04-01 实施:
ASTM E2368-2004e1 应变控制热力疲劳试验的标准规程
简介:In the utilization of structural materials in elevated temperature environments, components that are susceptible to fatigue damage may experience some form of simultaneously varying thermal and mechanical forces throughout a given cycle. These conditions are often of critical concern because they combine temperature dependent and cycle dependent (fatigue) damage mechanisms with varying severity relating to the phase relationship between cyclic temperature and cyclic mechanical strain. Such effects can be found to influence the evolution of microstructure, micromechanisms of degradation, and a variety of other phenomenological processes that ultimately affect cyclic life. The strain-controlled thermomechanical fatigue test is often used to investigate the effects of simultaneously varying thermal and mechanical loadings under idealized conditions, where cyclic theoretically uniform temperature and strain fields are externally imposed and controlled throughout the gage section of the specimen.1.1 This practice covers the determination of thermomechanical fatigue (TMF) properties of materials under uniaxially loaded strain-controlled conditions. A "thermomechanical" fatigue cycle is here defined as a condition where uniform temperature and strain fields over the specimen gage section are simultaneously varied and independently controlled. This practice is intended to address TMF testing performed in support of such activities as materials research and development, mechanical design, process and quality control, product performance, and failure analysis. While this practice is specific to strain-controlled testing, many sections will provide useful information for force-controlled or stress-controlled TMF testing.1.2 This practice allows for any maximum and minimum values of temperature and mechanical strain, and temperature-mechanical strain phasing, with the restriction being that such parameters remain cyclically constant throughout the duration of the test. No restrictions are placed on environmental factors such as pressure, humidity, environmental medium, and others, provided that they are controlled throughout the test, do not cause loss of or change in specimen dimensions in time, and are detailed in the data report.1.3 The use of this practice is limited to specimens and does not cover testing of full-scale components, structures, or consumer products.
信息:ICS:19.060 (Mechanical testing) CCS:A40 发布:2004 实施:
ASTM E2368-10(2017) 应变控制热机械疲劳试验的标准操作规程
简介:
信息:ICS:19.060 CCS: 发布:2017-11-01 实施:
ISO 24999:2008 柔性多孔聚合材料——用恒应变法测定疲劳
简介:
信息:ICS:83.100 CCS: 发布:2008-06-23 实施:
ASTM E1949-03 金属接合电阻应变片的环境温度疲劳寿命的标准测试方法
简介:
信息:ICS:19.060 CCS: 发布:2003-09-10 实施:
BS ISO 12106-2017 金属材料. 疲劳试验. 轴向应变控制法
简介:
信息:ICS:77.040.10 CCS:H22;H23 发布:2017-03-31 实施:2017-03-31
ASTM E2207-08 用薄壁管状样品进行应变控制轴向扭转疲劳试验的标准实践
简介:
信息:ICS:19.060 CCS: 发布:2008-01-01 实施:
KS B ISO 4965-2003 轴向负荷疲劳试验机.动态力校准.应变测量技术
简介:이 규격은 시험기의 교정에 영향을 줄 수 있는 시험용 치구를 포함한 피로 시험기의 동하
信息:ICS:77.040.10 CCS:N71 发布:2003-07-11 实施:2003-07-11
ISO 12106:2017 金属材料 - 疲劳试验 - 轴向应变控制法
简介:
信息:ICS:77.040.10 CCS: 发布:2017-03-23 实施:
ASTM E2207-08(2013)e1 用薄壁管状样品进行应变控制轴向扭转疲劳试验的标准实践
简介:
信息:ICS:19.060 CCS: 发布:2008-01-01 实施:
ISO 12106:2003 金属材料——疲劳试验——轴向应变控制法
简介:
信息:ICS:77.040.10 CCS: 发布:2003-04-02 实施:
ISO 12106-2017 金属材料.疲劳试验.轴向应变控制法
简介:
信息:ICS:77.040.10 CCS:H22 发布:2017-03 实施:
AECMA PREN 3987-2007 航空航天系列.金属材料的试验方法 等幅控制应变低循环疲劳试验
简介:The present standard gives a selection of external diameters and thicknesses of tubes according to ISO 2964. These tubes shall be used for conveying fluids such as kerosen, oil, air, etc… for engine application.
信息:ICS:77.040.30 CCS:V11 发布:2007-07-01 实施:
ISO 12106-2003 金属材料.疲劳试验.轴向应变控制法
简介:This International Standard specifies a method of testing uniaxially loaded specimens under strain control at constant amplitude, uniform temperature and strain ratio Rε= -1.It can also be used as a guide for testing under other conditions.
信息:ICS:77.040.10 CCS:H22 发布:2003-03 实施:
ISO 12106-2017 金属材料.疲劳试验.轴向应变控制法
简介:
信息:ICS:77.040.10 CCS:H22 发布:2017-03 实施:
ASTM E739-91(2004)e1 线性或线性化应力寿命(
简介:
信息:ICS:19.060 CCS: 发布:2006-05-01 实施:
ASTM E2207-02 用薄壁管状样品进行应变控制轴向扭转疲劳试验的标准实践
简介:
信息:ICS:19.060 CCS: 发布:2002-05-10 实施:
我们的实力
部分实验仪器




合作客户
注意:因业务调整,暂不接受个人委托测试望见谅。