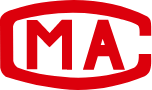



ASTM E647.相关标准参考信息
ASTM E647-15 测量疲劳裂纹扩展速率的标准试验方法
简介:
信息:ICS:77.040.10 CCS: 发布:2015-05-01 实施:
ASTM E647-05 测量疲劳裂纹扩展速率的标准试验方法
简介:
信息:ICS:77.040.10 CCS: 发布:2005-06-15 实施:
简介: 信息:
ASTM E647-2015 测量疲劳裂纹扩展速率的标准试验方法
简介:5.1x00a0;Fatigue crack growth rate expressed as a function of crack-tip stress-intensity factor range, d a/dN versus x0394;K, characterizes a material's resistance to stable crack extension under cyclic loading. Background information on the ration-ale for employing linear elastic fracture mechanics to analyze fatigue crack growth rate data is given in Refs (1)5 and (2). 5.1.1x00a0;In innocuous (inert) environments fatigue crack growth rates are primarily a function of x0394;K and force ratio, R, or Kmax and R (Note 1). Temperature and aggressive environments can significantly affect da/ dN versus x0394;K, and in many cases accentuate R-effects and introduce effects of other loading variables such as cycle frequency and waveform. Attention needs to be given to the proper selection and control of these variables in research studies and in the generation of design data. Note 1:x00a0;x0394;K, Kmax, and R are not independent of each other. Specification of any two of these variables is sufficient to define the loading condition. It is customary to specify one of the stress-intensity parameters (x0394;K or Kmax) along with the force ratio, R. 5.1.2x00a0;Expressing da/dN as a function of x0394;K provides results that are independent of planar geometry, thus enabling exchange and comparison of data obtained from a variety of specimen configurations and loading conditi......
信息:ICS:77.040.10 CCS: 发布:2015 实施:
ASTM E647-2005 测量疲劳裂缝增长率的标准试验方法
简介:1.1 This test method178; covers the determination of fatigue crack growth rates from near-threshold to Kmax controlled instability. Results are expressed in terms of the crack-tip stress-intensity factor range (916; K), defined by the theory of linear elasticity.1.2 Several different test procedures are provided, the optimum test procedure being primarily dependent on the magnitude of the fatigue crack growth rate to be measured.1.3 Materials that can be tested by this test method are not limited by thickness or by strength so long as specimens are of sufficient thickness to preclude buckling and of sufficient planar size to remain predominantly elastic during testing.1.4 A range of specimen sizes with proportional planar dimensions is provided, but size is variable to be adjusted for yield strength and applied force. Specimen thickness may be varied independent of planar size.1.5 The details of the various specimens and test configurations are shown in Annex A1-Annex A3. Specimen configurations other than those contained in this method may be used provided that well-established stress-intensity factor calibrations are available and that specimens are of sufficient planar size to remain predominantly elastic during testing.1.6 Residual stress/crack closure may significantly influence the fatigue crack growth rate data, particularly at low stress-intensity factors and low stress ratios, although such variables are not incorporated into the computation of 916;K.1.7 Values stated in SI units are to be regarded as the standard. Values given in parentheses are for information only.1.8 This test method is divided into two main parts. The first part gives general information concerning the recommendations and requirements for fatigue crack growth rate testing. The second part is composed of annexes that describe the special requirements for various specimen configurations, special requirements for testing in aqueous environments, and procedures for non-visual crack size determination. In addition, there are appendices that cover techniques for calculating da/dN, determining fatigue crack opening force, and guidelines for measuring the growth of small fatigue cracks. General information and requirements common to all specimen types are listed as follows:SectionReferenced Documents2Terminology3Summary of Use4Significance and Use5Apparatus6Specimen Configuration, Size, and Preparation7Procedure8Calculations and Interpretation of Results9Report10Precision and Bias11Special Requirements for Testing in Aqueous EnvironmentsAnnex A4Guidelines for Use of Compliance to Determine Crack SizeAnnex A5Guidelines for Electric Potential Difference Determination of Crack SizeAnnex A6Recommended Data Reduction TechniquesAppendix X1Recommended Practice for Determination of Fatigue Crack Opening Force From ComplianceAppendix X2Guidelines for Measuring the Growth Rates Of Small Fatigue CracksAppendix X31.9 Special requirements for the various specimen configurations appear in the following order:The Compact Tension SpecimenAnnex A1The Middle Tension SpecimenAnnex A2The Eccentrically-Loaded Single Edge Crack Tension SpecimenAnnex A31.10 This standard does not purport to address all of the safety concerns, if any, associated with its use. It is the res......
信息:ICS:77.040.10 (Mechanical testing of metals) CCS:H22 发布:2005 实施:
简介: 信息:
ASTM E647-2015e1
简介:5.1x00a0;Fatigue crack growth rate expressed as a function of crack-tip stress-intensity factor range, d a/dN versus x0394;K, characterizes a material's resistance to stable crack extension under cyclic loading. Background information on the ration-ale for employing linear elastic fracture mechanics to analyze fatigue crack growth rate data is given in Refs (1)5 and (2). 5.1.1x00a0;In innocuous (inert) environments fatigue crack growth rates are primarily a function of x0394;K and force ratio, R, or Kmax and R (Note 1). Temperature and aggressive environments can significantly affect da/ dN versus x0394;K, and in many cases accentuate R-effects and introduce effects of other loading variables such as cycle frequency and waveform. Attention needs to be given to the proper selection and control of these variables in research studies and in the generation of design data. Note 1:x00a0;x0394;K, Kmax, and R are not independent of each other. Specification of any two of these variables is sufficient to define the loading condition. It is customary to specify one of the stress-intensity parameters (x0394;K or Kmax) along with the force ratio, R. 5.1.2x00a0;Expressing da/dN as a function of x0394;K provides results that are independent of planar geometry, thus enabling exchange and comparison of data obtained from a variety of specimen configurations and loading conditi......
信息:ICS:77.040.10 CCS: 发布:2015 实施:
ASTM E647-95 测量疲劳裂纹扩展速率的标准试验方法
简介:
信息:ICS:77.040.10 CCS: 发布:2000-12-10 实施:
简介: 信息:
ASTM E647-13ae1 测量疲劳裂纹扩展速率的标准试验方法
简介:
信息:ICS:77.040.10 CCS: 发布:2013-10-15 实施:
ASTM E647-00 测量疲劳裂纹扩展速率的标准试验方法
简介:
信息:ICS:77.040.10 CCS: 发布:2000-12-10 实施:
简介: 信息:
ASTM E647-13a 测量疲劳裂纹扩展速率的标准试验方法
简介:
信息:ICS:77.040.10 CCS: 发布:2013-10-15 实施:
ASTM E647-99 测量疲劳裂纹扩展速率的标准试验方法
简介:
信息:ICS:77.040.10 CCS: 发布:2000-12-10 实施:
简介: 信息:
ASTM E647-13 测量疲劳裂纹扩展速率的标准试验方法
简介:
信息:ICS:77.040.10 CCS: 发布:2013-01-15 实施:
ASTM E647-2000 疲劳裂缝增长率测量的标准试验方法
简介:1.1 This test method covers the determination of fatigue crack growth rates from near-threshold to Kmax controlled instability. Results are expressed in terms of the crack-tip stress-intensity factor range ( K), defined by the theory of linear elasticity.1.2 Several different test procedures are provided, the optimum test procedure being primarily dependent on the magnitude of the fatigue crack growth rate to be measured.1.3 Materials that can be tested by this test method are not limited by thickness or by strength so long as specimens are of sufficient thickness to preclude buckling and of sufficient planar size to remain predominantly elastic during testing.1.4 A range of specimen sizes with proportional planar dimensions is provided, but size is variable to be adjusted for yield strength and applied force. Specimen thickness may be varied independent of planar size.1.5 The details of the various specimens and test configurations are shown in Annex A1 - Annex A3. Specimen configurations other than those contained in this method may be used provided that well-established stress-intensity factor calibrations are available and that specimens are of sufficient planar size to remain predominantly elastic during testing.1.6 Residual stress/crack closure may significantly influence the fatigue crack growth rate data, particularly at low stress-intensity factors and low stress ratios, although such variables are not incorporated into the computation of K.1.7 Values stated in SI units are to be regarded as the standard. Values given in parentheses are for information only.1.8 This test method is divided into two main parts. The first part gives general information concerning the recommendations and requirements for fatigue crack growth rate testing. The second part is composed of annexes that describe the special requirements for various specimen configurations, special requirements for testing in aqueous environments, and procedures for non-visual crack size determination. In addition, there are appendices that cover techniques for calculating da/dN, determining fatigue crack opening force, and guidelines for measuring the growth of small fatigue cracks. General information and requirements common to all specimen types are listed as follows: SectionReferenced Documents2Terminology3Summary of Use4Significance and Use5Apparatus6Specimen Configuration, Size, and Preparation7Procedure8Calculations and Interpretation of Results9Report10Precision and Bias11Special Requirements for Testing in Aqueous EnvironmentsAnnex A4Guidelines for Use of Compliance to Determine Crack SizeAnnex A5Guidelines for Electric Potential Difference Determination of Crack SizeAnnex A6Recommended Data Reduction TechniquesAppendix X1Recommended Practice for Determination of Fatigue Crack Opening Force From ComplianceAppendix X2Guidelines for Measuring the Growth Rates Of Small Fatigue CracksAppendix X31.9 Special requirements for the various specimen configurations appear in the following order:The Compact Tension SpecimenAnnex A1The Middle Tension SpecimenAnnex A2The Eccentrically-Loaded Single Edge Crack Tension SpecimenAnnex A31.10 This standard does not purport to address all of the safety concerns, if any, associated with its use. It is the responsibility ......
信息:ICS:77.040.10 (Mechanical testing of metals) CCS:H22 发布:2000 实施:
简介: 信息:
ASTM E647-13e1 测量疲劳裂纹扩展速率的标准试验方法
简介:
信息:ICS:77.040.10 CCS: 发布:2013-01-15 实施:
ASTM E647-1999 疲劳裂缝增长率测量的标准试验方法
简介:1.1 This test method covers the determination of fatigue crack growth rates from near-threshold to Kmax controlled instability. Results are expressed in terms of the crack-tip stress-intensity factor range ( K), defined by the theory of linear elasticity.1.2 Several different test procedures are provided, the optimum test procedure being primarily dependent on the magnitude of the fatigue crack growth rate to be measured.1.3 Materials that can be tested by this test method are not limited by thickness or by strength so long as specimens are of sufficient thickness to preclude buckling and of sufficient planar size to remain predominantly elastic during testing.1.4 A range of specimen sizes with proportional planar dimensions is provided, but size is variable to be adjusted for yield strength and applied force. Specimen thickness may be varied independent of planar size.1.5 The details of the various specimens and test configurations are shown in Annex A1 - Annex A3. Specimen configurations other than those contained in this method may be used provided that well-established stress-intensity factor calibrations are available and that specimens are of sufficient planar size to remain predominantly elastic during testing.1.6 Residual stress/crack closure may significantly influence the fatigue crack growth rate data, particularly at low stress-intensity factors and low stress ratios, although such variables are not incorporated into the computation of K.1.7 Values stated in SI units are to be regarded as the standard. Values given in parentheses are for information only.1.8 This test method is divided into two main parts. The first part gives general information concerning the recommendations and requirements for fatigue crack growth rate testing. The second part is composed of annexes that describe the special requirements for various specimen configurations, special requirements for testing in aqueous environments, and procedures for non-visual crack size determination. In addition, there are appendices that cover techniques for calculating da/dN, determining fatigue crack opening force, and guidelines for measuring the growth of small fatigue cracks. General information and requirements common to all specimen types are listed as follows: SectionReferenced Documents2Terminology3Summary of Use4Significance and Use5Apparatus6Specimen Configuration, Size, and Preparation7Procedure8Calculations and Interpretation of Results9Report10Precision and Bias11Special Requirements for Testing in Aqueous EnvironmentsAnnex A4Guidelines for Use of Compliance to Determine Crack SizeAnnex A5Guidelines for Electric Potential Difference Determination of Crack SizeAnnex A6Recommended Data Reduction TechniquesAppendix X1Recommended Practice for Determination of Fatigue Crack Opening Force From ComplianceAppendix X2Guidelines for Measuring the Growth Rates Of Small Fatigue CracksAppendix X31.9 Special requirements for the various specimen configurations appear in the following order:The Compact Tension SpecimenAnnex A1The Middle Tension SpecimenAnnex A2The Eccentrically-Loaded Single Edge Crack Tension SpecimenAnnex A31.10 This standard does not purport to address all of the safety concerns, if any, associated with its use. It is the responsibility ......
信息:ICS:77.040.10 (Mechanical testing of metals) CCS:H22 发布:1999 实施:
简介: 信息:
ASTM E647-2013a 测量疲劳裂纹扩展速率的标准试验方法
简介:5.1x00a0;Fatigue crack growth rate expressed as a function of crack-tip stress-intensity factor range, d a/dN versus x0394;K, characterizes a materialx0027;s resistance to stable crack extension under cyclic loading. Background information on the ration-ale for employing linear elastic fracture mechanics to analyze fatigue crack growth rate data is given in Refs (1)5 and (2). 5.1.1x00a0;In innocuous (inert) environments fatigue crack growth rates are primarily a function of x0394;K and force ratio, R, or K max and R (Note 1). Temperature and aggressive environments can significantly affect da/ dN versus x0394;K, and in many cases accentuate R-effects and introduce effects of other loading variables such as cycle frequency and waveform. Attention needs to be given to the proper selection and control of these variables in research studies and in the generation of design data.Note 1x2014;x0394;K, Kmax, and R are not independent of each other. Specification of any two of these variables is sufficient to define the loading condition. It is customary to specify one of the stress-intensity parameters (x0394;K or Kmax) along with the force ratio, R. 5.1.2x00a0;Expressing da/dN as a function of x0394;K provides results that are independent of planar geometry, thus enabling exchange and comparison of data obtained from a variety of specimen configurations and loading conditions. Moreover, this feature enables d a/dN versus x0394;K data to be utilized in the design and evaluation of engineering structures. The concept of similitude is assumed, which implies that cracks of differing lengths subjected to the same nominal x0394;K will advance by equal increments of crack extension per cycle. 5.1.3x00a0;Fatigue crack growth rate data are not always geometry-independent in the strict sense since thickness effects sometimes occur. However, data on the influence of thickness on fatigue crack growth rate are mixed. Fat......
信息:ICS:77.040.10 (Mechanical testing of metals) CCS: 发布:2013 实施:
ASTM E647-1995 疲劳裂缝增长率测量的标准试验方法
简介:1.1 This test method covers the determination of fatigue crack growth rates from near-threshold to Kmax controlled instability. Results are expressed in terms of the crack-tip stress-intensity factor range ( K), defined by the theory of linear elasticity.1.2 Several different test procedures are provided, the optimum test procedure being primarily dependent on the magnitude of the fatigue crack growth rate to be measured.1.3 Materials that can be tested by this test method are not limited by thickness or by strength so long as specimens are of sufficient thickness to preclude buckling and of sufficient planar size to remain predominantly elastic during testing.1.4 A range of specimen sizes with proportional planar dimensions is provided, but size is variable to be adjusted for yield strength and applied force. Specimen thickness may be varied independent of planar size.1.5 The details of the various specimens and test configurations are shown in Annex A1 - Annex A3. Specimen configurations other than those contained in this method may be used provided that well-established stress-intensity factor calibrations are available and that specimens are of sufficient planar size to remain predominantly elastic during testing.1.6 Residual stress/crack closure may significantly influence the fatigue crack growth rate data, particularly at low stress-intensity factors and low stress ratios, although such variables are not incorporated into the computation of K.1.7 Values stated in SI units are to be regarded as the standard. Values given in parentheses are for information only.1.8 This test method is divided into two main parts. The first part gives general information concerning the recommendations and requirements for fatigue crack growth rate testing. The second part is composed of annexes that describe the special requirements for various specimen configurations, special requirements for testing in aqueous environments, and procedures for non-visual crack size determination. In addition, there are appendices that cover techniques for calculating da/dN, determining fatigue crack opening force, and guidelines for measuring the growth of small fatigue cracks. General information and requirements common to all specimen types are listed as follows: SectionReferenced Documents2Terminology3Summary of Use4Significance and Use5Apparatus6Specimen Configuration, Size, and Preparation7Procedure8Calculations and Interpretation of Results9Report10Precision and Bias11Special Requirements for Testing in Aqueous EnvironmentsAnnex A4Guidelines for Use of Compliance to Determine Crack SizeAnnex A5Guidelines for Electric Potential Difference Determination of Crack SizeAnnex A6Recommended Data Reduction TechniquesAppendix X1Recommended Practice for Determination of Fatigue Crack Opening Force From ComplianceAppendix X2Guidelines for Measuring the Growth Rates Of Small Fatigue CracksAppendix X31.9 Special requirements for the various specimen configurations appear in the following order:The Compact Tension SpecimenAnnex A1The Middle Tension SpecimenAnnex A2The Eccentrically-Loaded Single Edge Crack Tension SpecimenAnnex A31.10 This standard does not purport to address all of the safety concerns, if any, associated with its use. It is the responsibility ......
信息:ICS:77.040.10 (Mechanical testing of metals) CCS:H22 发布:1995 实施:
简介: 信息:
ASTM E647-2013ae1 测量疲劳裂纹扩展速率的标准试验方法
简介:5.1x00a0;Fatigue crack growth rate expressed as a function of crack-tip stress-intensity factor range, d a/dN versus x0394;K, characterizes a materialx0027;s resistance to stable crack extension under cyclic loading. Background information on the ration-ale for employing linear elastic fracture mechanics to analyze fatigue crack growth rate data is given in Refs (1)5 and (2). 5.1.1x00a0;In innocuous (inert) environments fatigue crack growth rates are primarily a function of x0394;K and force ratio, R, or Kmax and R (Note 1). Temperature and aggressive environments can significantly affect da/ dN versus x0394;K, and in many cases accentuate R-effects and introduce effects of other loading variables such as cycle frequency and waveform. Attention needs to be given to the proper selection and control of these variables in research studies and in the generation of design data. Note 1:x00a0;x0394;K, Kmax, and R are not independent of each other. Specification of any two of these variables is sufficient to define the loading condition. It is customary to specify one of the stress-intensity parameters (x0394;K or Kmax) along with the force ratio, R. 5.1.2x00a0;Expressing da/dN as a function of x0394;K provides results that are independent of planar geometry, thus enabling exchange and comparison of data obtained from a variety of specimen configurations and loading conditions. ......
信息:ICS:77.040.10 (Mechanical testing of metals) CCS: 发布:2013 实施:
ASTM E647-15e1 ASTM E647-15e1
简介:
信息:ICS:/ CCS:/ 发布:0000-00-00 实施:0000-00-00
简介: 信息:
ASTM E647-2013 测量疲劳裂缝增长率的标准试验方法
简介:Fatigue crack growth rate expressed as a function of crack-tip stress-intensity factor range, da/dN versus x0394;K, characterizes a materialx0027;s resistance to stable crack extension under cyclic loading. Background information on the ration-ale for employing linear elastic fracture mechanics to analyze fatigue crack growth rate data is given in Refs (1) and (2). In innocuous (inert) environments fatigue crack growth rates are primarily a function of x0394;K and force ratio, R, or Kmax and R (Note 1). Temperature and aggressive environments can significantly affect da/dN versus x0394;K, and in many cases accentuate R-effects and introduce effects of other loading variables such as cycle frequency and waveform. Attention needs to be given to the proper selection and control of these variables in research studies and in the generation of design data. Note 18212;x0394;K, Kmax, and R are not independent of each other. Specification of any two of these variables is sufficient to define the loading condition. It is customary to specify one of the stress-intensity parameters (x0394;K or Kmax) along with the force ratio, R. Expressing da/dN as a function of x0394;K provides results that are independent of planar geometry, thus enabling exchange and comparison of data obtained from a variety of specimen configurations and loading conditions. Moreover, this feature enables da/dN versus x0394;K data to be utilized in the design and evaluation of engineering structures. The concept of similitude is assumed, which implies that cracks of differing lengths subjected to the same nominal x0394;K will advance by equal increments of crack extension per cycle. Fatigue crack growth rate data are not always geometry-independent in the strict sense since thickness effects sometimes occur. However, data on the influence of thickness on fatigue crack growth rate are mixed. Fatigue crack growth rates over a wide range of x0394;K have been reported to either increase, decrease, or remain unaffected as specimen thickness is increased. Thickness effects can also interact with other variables such as environment and heat treatment. For example, materials may exhibit thickness effects over the terminal range of da/dN versus x0394;K, which are associated with either nominal yielding (Note 2) or as Kmax approaches the material fracture toughness. The potential influence of specimen thickness should be considered when generating data for research or design. Note 28212;This condition should be avoided in tests that conform to the specimen size requirements listed in the appropriate specimen annex. Residual ......
信息:ICS:77.040.10 (Mechanical testing of metals) CCS: 发布:2013 实施:
简介: 信息:
简介: 信息:
ASTM E647-2013e1 测量疲劳裂缝增长率的标准试验方法
简介:5.1x00a0;Fatigue crack growth rate expressed as a function of crack-tip stress-intensity factor range, d a/dN versus x0394;K, characterizes a materialx0027;s resistance to stable crack extension under cyclic loading. Background information on the ration-ale for employing linear elastic fracture mechanics to analyze fatigue crack growth rate data is given in Refs (1)5 and (2). 5.1.1x00a0;In innocuous (inert) environments fatigue crack growth rates are primarily a function of x0394;K and force ratio, R, or K max and R (Note 1). Temperature and aggressive environments can significantly affect da/ dN versus x0394;K, and in many cases accentuate R-effects and introduce effects of other loading variables such as cycle frequency and waveform. Attention needs to be given to the proper selection and control of these variables in research studies and in the generation of design data.Note 1x2014;x0394;K, Kmax, and R are not independent of each other. Specification of any two of these variables is sufficient to define the loading condition. It is customary to specify one of the stress-intensity parameters (x0394;K or Kmax) along with the force ratio, R. 5.1.2x00a0;Expressing da/dN as a function of x0394;K provides results that are independent of planar geometry, thus enabling exchange and comparison of data obtained from a variety of specimen configurations and loading conditions. Moreover, this feature enables d a/dN versus x0394;K data to be utilized in the design and evaluation of engineering structures. The concept of similitude is assumed, which implies that cracks of differing lengths subjected to the same nominal x0394;K will advance by equal increments of crack extension per cycle.
信息:ICS:77.040.10 (Mechanical testing of metals) CCS: 发布:2013 实施:
简介: 信息:
简介: 信息:
ASTM E647-2012
简介:Fatigue crack growth rate expressed as a function of crack-tip stress-intensity factor range, da/dN versus x0394;K, characterizes a material''s resistance to stable crack extension under cyclic loading. Background information on the ration-ale for employing linear elastic fracture mechanics to analyze fatigue crack growth rate data is given in Refs (1) and (2). In innocuous (inert) environments fatigue crack growth rates are primarily a function of x0394;K and force ratio, R, or Kmax and R (Note 1). Temperature and aggressive environments can significantly affect da/dN versus x0394;K, and in many cases accentuate R-effects and introduce effects of other loading variables such as cycle frequency and waveform. Attention needs to be given to the proper selection and control of these variables in research studies and in the generation of design data. Note 18212;x0394;K, Kmax, and R are not independent of each other. Specification of any two of these variables is sufficient to define the loading condition. It is customary to specify one of the stress-intensity parameters (x0394;K or Kmax) along with the force ratio, R. Expressing da/dN as a function of x0394;K provides results that are independent of planar geometry, thus enabling exchange and comparison of data obtained from a variety of specimen configurations and loading conditions. Moreover, this feature enables da/dN versus x0394;K data to be utilized in the design and evaluation of engineering structures. The concept of similitude is assumed, which implies that cracks of differing lengths subjected to the same nominal x0394;K will advance by equal increments of crack extension per cycle. Fatigue crack growth rate data are not always geometry-independent in the strict sense since thickness effects sometimes occur. However, data on the influence of thickness on fatigue crack growth rate are mixed. Fatigue crack growth rates over a wide range of x0394;K have been reported to either increase, decrease, or remain unaffected as specimen thickness is increased. Thickness effects can also interact with other variables such as environment and heat treatment. For example, materials may exhibit thickness effects over the terminal range of da/dN versus x0394;K, which are associated with either nominal yielding (Note 2) or as Kmax approaches the material fracture toughness. The potential influence of specimen thickness should be considered when generating data for research or design. Note 28212;This condition should be avoided in tests that conform to the specimen size requiremen......
信息:ICS:77.040.10 CCS: 发布:2012 实施:
简介: 信息:
简介: 信息:
ASTM E647-11 测量疲劳裂纹扩展速率的标准试验方法
简介:
信息:ICS:77.040.10 CCS: 发布:2011-05-01 实施:
简介: 信息:
简介: 信息:
ASTM E647-2011e1 疲劳裂纹扩展速率测量的标准试验方法
简介:Fatigue crack growth rate expressed as a function of crack-tip stress-intensity factor range, da/dN versus x0394;K, characterizes a material''s resistance to stable crack extension under cyclic loading. Background information on the ration-ale for employing linear elastic fracture mechanics to analyze fatigue crack growth rate data is given in Refs (1) and (2). In innocuous (inert) environments fatigue crack growth rates are primarily a function of x0394;K and force ratio, R, or Kmax and R (Note 1). Temperature and aggressive environments can significantly affect da/dN versus x0394;K, and in many cases accentuate R-effects and introduce effects of other loading variables such as cycle frequency and waveform. Attention needs to be given to the proper selection and control of these variables in research studies and in the generation of design data. Note 18212;x0394;K, Kmax, and R are not independent of each other. Specification of any two of these variables is sufficient to define the loading condition. It is customary to specify one of the stress-intensity parameters (x0394;K or Kmax) along with the force ratio, R. Expressing da/dN as a function of x0394;K provides results that are independent of planar geometry, thus enabling exchange and comparison of data obtained from a variety of specimen configurations and loading conditions. Moreover, this feature enables da/dN versus x0394;K data to be utilized in the design and evaluation of engineering structures. The concept of similitude is assumed, which implies that cracks of differing lengths subjected to the same nominal x0394;K will advance by equal increments of crack extension per cycle. Fatigue crack growth rate data are not always geometry-independent in the strict sense since thickness effects sometimes occur. However, data on the influence of thickness on fatigue crack growth rate are mixed. Fatigue crack growth rates over a wide range of x0394;K have been reported to either increase, decrease, or remain unaffected as specimen thickness is increased. Thickness effects can also interact with other variables such as environment and heat treatment. For example, materials may exhibit thickness effects over the terminal range of da/dN versus x0394;K, which are associated with either nominal yielding (Note 2) or as Kmax approaches the material fracture toughness. The potential influence of specimen thickness should be considered when generating data for research or design. Note 28212;This condition should be avoided in tests that conform to the specimen size requiremen......
信息:ICS:77.040.10 (Mechanical testing of metals) CCS:H22 发布:2011 实施:
简介: 信息:
简介: 信息:
ASTM E647-2011 疲劳裂缝增大率测量的标准试验方法
简介:Fatigue crack growth rate expressed as a function of crack-tip stress-intensity factor range, da/dN versus x0394;K, characterizes a material''s resistance to stable crack extension under cyclic loading. Background information on the ration-ale for employing linear elastic fracture mechanics to analyze fatigue crack growth rate data is given in Refs (1) and (2). In innocuous (inert) environments fatigue crack growth rates are primarily a function of x0394;K and force ratio, R, or Kmax and R (Note 1). Temperature and aggressive environments can significantly affect da/dN versus x0394;K, and in many cases accentuate R-effects and introduce effects of other loading variables such as cycle frequency and waveform. Attention needs to be given to the proper selection and control of these variables in research studies and in the generation of design data. Note 18212;x0394;K, Kmax, and R are not independent of each other. Specification of any two of these variables is sufficient to define the loading condition. It is customary to specify one of the stress-intensity parameters (x0394;K or Kmax) along with the force ratio, R. Expressing da/dN as a function of x0394;K provides results that are independent of planar geometry, thus enabling exchange and comparison of data obtained from a variety of specimen configurations and loading conditions. Moreover, this feature enables da/dN versus x0394;K data to be utilized in the design and evaluation of engineering structures. The concept of similitude is assumed, which implies that cracks of differing lengths subjected to the same nominal x0394;K will advance by equal increments of crack extension per cycle. Fatigue crack growth rate data are not always geometry-independent in the strict sense since thickness effects sometimes occur. However, data on the influence of thickness on fatigue crack growth rate are mixed. Fatigue crack growth rates over a wide range of x0394;K have been reported to either increase, decrease, or remain unaffected as specimen thickness is increased. Thickness effects can also interact with other variables such as environment and heat treatment. For example, materials may exhibit thickness effects over the terminal range of da/dN versus x0394;K, which are associated with either nominal yielding (Note 2) or as Kmax approaches the material fracture toughness. The potential influence of specimen thickness should be considered when generating data for research or design. Note 28212;This condition should be avoided in tests that conform to the specimen size requiremen......
信息:ICS:77.040.10 (Mechanical testing of metals) CCS:H22 发布:2011 实施:
简介: 信息:
简介: 信息:
ASTM E647-11e1 测量疲劳裂纹扩展速率的标准试验方法
简介:
信息:ICS:77.040.10 CCS: 发布:2008-04-01 实施:
简介: 信息:
简介: 信息:
ASTM E647-08 测量疲劳裂纹扩展速率的标准试验方法
简介:
信息:ICS:77.040.10 CCS: 发布:2008-04-01 实施:
简介: 信息:
简介: 信息:
ASTM E647-08e1 测量疲劳裂纹扩展速率的标准试验方法
简介:
信息:ICS:77.040.10 CCS: 发布:2008-04-01 实施:
简介: 信息:
简介: 信息:
ASTM E647-2008e1 疲劳裂缝增大率测量用测试方法
简介:Fatigue crack growth rate expressed as a function of crack-tip stress-intensity factor range, da/dN versus x0394;K, characterizes a material''s resistance to stable crack extension under cyclic loading. Background information on the ration-ale for employing linear elastic fracture mechanics to analyze fatigue crack growth rate data is given in Refs (1) and (2).1.1 This test method covers the determination of fatigue crack growth rates from near-threshold to Kmax controlled instability. Results are expressed in terms of the crack-tip stress-intensity factor range (x0394;K), defined by the theory of linear elasticity. 1.2 Several different test procedures are provided, the optimum test procedure being primarily dependent on the magnitude of the fatigue crack growth rate to be measured. 1.3 Materials that can be tested by this test method are not limited by thickness or by strength so long as specimens are of sufficient thickness to preclude buckling and of sufficient planar size to remain predominantly elastic during testing. 1.4 A range of specimen sizes with proportional planar dimensions is provided, but size is variable to be adjusted for yield strength and applied force. Specimen thickness may be varied independent of planar size. 1.5 The details of the various specimens and test configurations are shown in Annex A1-Annex A3. Specimen configurations other than those contained in this method may be used provided that well-established stress-intensity factor calibrations are available and that specimens are of sufficient planar size to remain predominantly elastic during testing. 1.6 Residual stress/crack closure may significantly influence the fatigue crack growth rate data, particularly at low stress-intensity factors and low stress ratios, although such variables are not incorporated into the computation of x0394;K. 1.7 Values stated in SI units are to be regarded as the standard. Values given in parentheses are for information only. 1.8 This test method is divided into two main parts. The first part gives general information concerning the recommendations and requirements for fatigue crack growth rate testing. The second part is composed of annexes that describe the special requirements for various specimen configurations, special requirements for testing in aqueous environments, and procedures for non-visual crack size determination. In addition, there are appendices that cover techniques for calculating da/dN, determining fatigue crack opening force, and guidelines for measuring the growth of small fatigue cracks. General information and requirements common to all specimen types are listed as follows:
信息:ICS:77.040.10 (Mechanical testing of metals) CCS:H22 发布:2008 实施:
简介: 信息:
简介: 信息:
ASTM E647-2008
简介:Fatigue crack growth rate expressed as a function of crack-tip stress-intensity factor range, da/dN versus x0394;K, characterizes a material''s resistance to stable crack extension under cyclic loading. Background information on the ration-ale for employing linear elastic fracture mechanics to analyze fatigue crack growth rate data is given in Refs (1) and (2). In innocuous (inert) environments fatigue crack growth rates are primarily a function of x0394;K and force ratio, R, or Kmax and R (Note 1). Temperature and aggressive environments can significantly affect da/dN versus x0394;K, and in many cases accentuate R-effects and introduce effects of other loading variables such as cycle frequency and waveform. Attention needs to be given to the proper selection and control of these variables in research studies and in the generation of design data. Note 18212;x0394;K, Kmax, and R are not independent of each other. Specification of any two of these variables is sufficient to define the loading condition. It is customary to specify one of the stress-intensity parameters (x0394;K or Kmax) along with the force ratio, R. Expressing da/dN as a function of x0394;K provides results that are independent of planar geometry, thus enabling exchange and comparison of data obtained from a variety of specimen configurations and loading conditions. Moreover, this feature enables da/dN versus x0394;K data to be utilized in the design and evaluation of engineering structures. The concept of similitude is assumed, which implies that cracks of differing lengths subjected to the same nominal x0394;K will advance by equal increments of crack extension per cycle. Fatigue crack growth rate data are not always geometry-independent in the strict sense since thickness effects sometimes occur. However, data on the influence of thickness on fatigue crack growth rate are mixed. Fatigue crack growth rates over a wide range of x0394;K have been reported to either increase, decrease, or remain unaffected as specimen thickness is increased. Thickness effects can also interact with other variables such as environment and heat treatment. For example, materials may exhibit thickness effects over the terminal range of da/dN versus x0394;K, which are associated with either nominal yielding (Note 2) or as Kmax approaches the material fracture toughness. The potential influence of specimen thickness should be considered when generating data for research or design. Note 28212;This condition should be avoided in tests that conform to the specimen size requirements listed in the appropr......
信息:ICS:77.040.10 (Mechanical testing of metals) CCS: 发布:2008 实施:
简介: 信息:
简介: 信息:
我们的实力
部分实验仪器




合作客户
注意:因业务调整,暂不接受个人委托测试望见谅。